Best borehole drilling company
As the best borehole drilling company in Kenya, we not only drill wells but thoroughly guide farmers on what is needed to procure borehole drilling services from Majitech Systems Limited. When the borehole is complete, we provide a borehole water pump that evacuates water to a storage unit. Our borehole pumps are submersible solar or electric types. In this piece, we provide a breakdown of the average cost of drilling a borehole in Kenya depending on the drilling method adopted
Requirements for drilling a borehole in Kenya
1. Hydro-geological survey
- Conduction of a hydro-geological survey to establish the water potential of an area. It provides; the point of drilling, depth, rock structure and the approximate amount of water present beneath. The latter is determined by assessing the yield of neighboring boreholes. This is a day’s job depending on the size of the area being surveyed. Geo-physical instruments are used to carry out this. The methods of survey are; resistivity method, vertical electrical sounding (VES), and horizontal electrical profiling (HEP)
- Review of the hydro-geological survey report
- The cost of a hydro-geological survey in Kenya is Kes 115,000. This cost covers payments for all permits and licenses
- The client must provide these documents for Water Resource Management Authority (WARMA) permit processing.
- The land title deed proving ownership or the sale agreement if the land transfer isn’t complete from the previous owner
- His/her identification card for individuals or the company registration certificate and CR12 for corporates
- The personal identification number (PIN) certificate
2. Licenses and permits
- Client submission of licenses and permits from; WARMA, National environmental management authority (NEMA), and the county government (if the county government must approve)
3. Site visit
- Physical site visit for logistics assessment
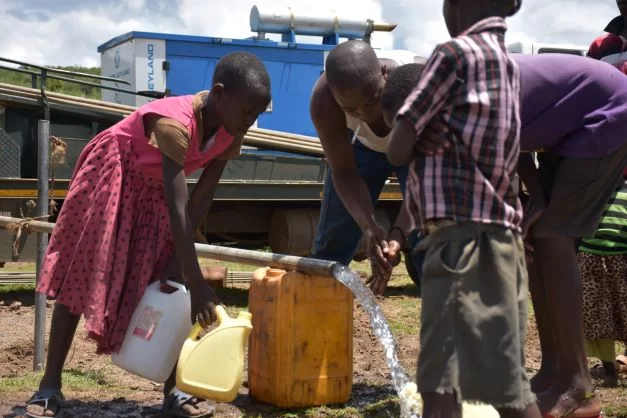
How to drill a borehole in Kenya; What the drilling cost entails
Mobilisation
This is the transfer to the well site of the rig, equipment, and labor. We cost mobilisation by distance. A borehole project 500kms away from our office will pay more for mobilisation than one that is 50kms away. Mobilisation costs allow for bush clearing and site preparation costs. This is to ready the borehole drilling site for the drilling rig and all other heavy equipment
Borehole drilling
This is the actual process of sinking a well in the ground in order to obtain water. The depth of sinking depends on the reading of the hydro-geological survey report. This report states the depth, amount of water expected, and the geological structure of the soil and rock underneath. The common size of the borehole well is 8 inches in diameter, but the surface section is 10 inches. Some wells are larger, going up to 14 inches in diameter
Casing
We line the walls of the borehole with mild steel or polyvinyl chloride (uPVC) casings. This is to keep the wall from collapsing throughout the lifetime of the borehole. We install 4mm – 4.5mm thick steel casings where the well has boulders, and where mud drilling is conducted. uPVC casings are installed in wells that lack boulders or that are rich in sand, and the water is highly saline. High salinity causes intense rusting on steel casings over time, hence the preference for uPVC casings in such wells
There are 2 types of casings
3.1. Continuous casings. They line the sections where the aquifer(s) is absent. They serve as water storage units because this is where the water is held. Surface casing are set from the mouth of the well downwards to the point where the walls are stronger. It could be as short as 3M, or as deep as 30M. Surface casings are 8″ in diameter
3.2. Slotted casings. They line the aquifer sections to allow water into the well. The slots are 1mm to 2mm in size
Our installation ratio of continuous and slotted casings is 70:30. This ensures maximum percolation of the water from the aquifer into the borehole
4. Graveling
It is the application of gravel sand between the borehole walls and the mild steel casings. Gravel filters soil and other impurities and keeps the casings firmly in position. Our gravel size is 2mm to 4mm, and well rounded
5. Flushing and capping
The well is cleaned of all chippings, a process referred to as flushing which is done after casing and also after graveling. Where casing is not carried out, flushing is done too. It is the process of pushing water within the well under intense pressure, then releasing it as a jet from the mouth of the well. Flushing allows optimal water flow from the aquifer to the well, and it precedes test pumping. In a high yielding borehole, the water within the well is used to clean it up. Where the well is low in yield, additional water is sourced for externally and added into the well.
After flushing, the well is sealed at the top with a cap to prevent dirt and other material from getting in
6. Test pumping
We draw out borehole water for 24 hours. This shows the yield of the well, recharge rate and water level. It is with this report that we determine the right solar or electric submersible water pump. Before the test pumping process, we determine the most suitable test pumping water pump and the right pipe diameter to use based on the estimated volume of water in the well. Our test pumping pipe diameter sizes are installed as;
Estimated Borehole Yield | Test Pumping Pipe Diameter |
0.5 – 10 cubic litres per hour | 1″ |
11 – 25 cubic litres per hour | 1-1/2″ |
> 25 cubic litres per hour | 2″ |
Having the right test pumping pump and pipe diameter size is key in achieving the right yield of the well
7. Water chemical analysis
Laboratory analysis of the chemical composition of the borehole water
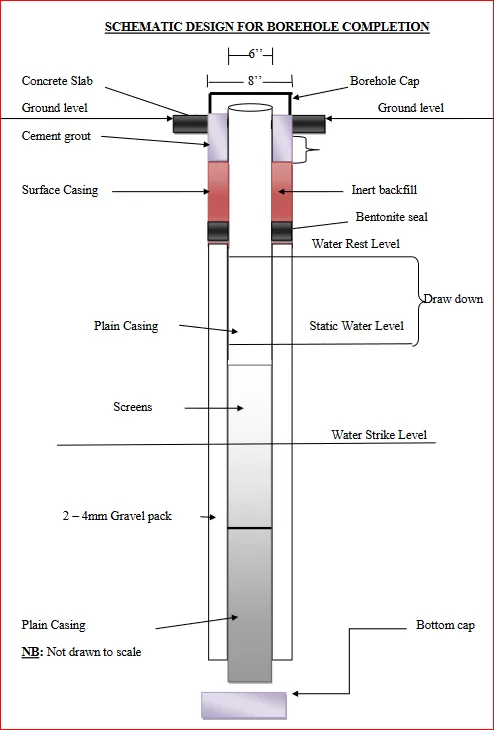